top of page

UNBREAKABLE
DYNAMIC CONDUCTOR
PREDICT THE LIFESPAN
Reliability Testing for Simulated User Scenarios
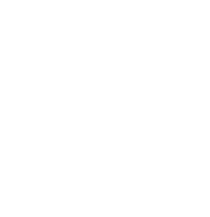
Bend test
BENDING
(bend test/swing test)
helps you to know how the wires behave when exposed to conditions like different temperature levels, pressure and moisture. When you do a bend test, you are trying to understand how our wires and cables perform when exposed to mechanical loads.
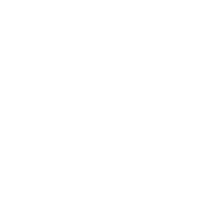