
Custom Flexible Aerospace Wire and Cable for Longer Flex Life
Understanding The Importance of Aerospace Wire and Cable in Harsh Conditions
Aerospace applications require highly reliable and durable wire and cable solutions due to the extreme conditions they operate in. Whether it's in commercial aircraft, military aircraft, or space exploration vehicles, aerospace wire and cable must withstand high levels of temperature, vibration, moisture, and electromagnetic interference. Additionally, they must be flexible enough to accommodate the constant movement and bending that occurs during flight or mission operations. In this article, we will explore the importance of aerospace wire and cable in such challenging conditions and highlight the benefits of using custom flexible wire and cable solutions.
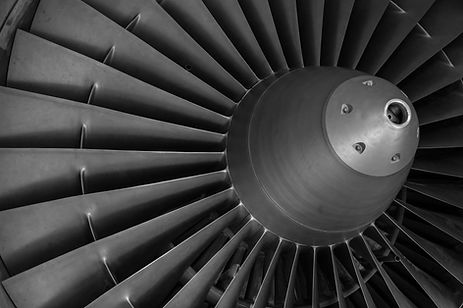
Understanding The Concept of Flexible Wire
Flexibility is a fundamental characteristic of wire and cable solutions that find application in a wide range of industries, including aerospace. Unlike rigid wires, flexible wires are designed to bend and conform to different shapes without compromising their performance or structural integrity. In this section, we explore the concept of flexible wire and its importance in various applications.
1
Versatility in Installations
Flexible wire offers unmatched versatility in installations. Its ability to bend and flex enables it to navigate through tight spaces and complex configurations, making it ideal for situations where rigid wires are impractical or impossible to use. This versatility extends to a multitude of industries, such as automotive, electronics, robotics, medical devices, and of course, aerospace.
2
Endurance under Dynamic Conditions
In aerospace and other dynamic environments, the ability of wires to withstand constant motion, vibrations, and mechanical stress is critical. Flexible wires are engineered to endure these demanding conditions without suffering damage or performance degradation. This characteristic ensures that electrical connections remain stable, even in the face of frequent movement and mechanical forces.
3
Flexibility without Sacrificing Performance
Despite their ability to bend and flex, flexible wires are designed to maintain their electrical properties and signal integrity. The materials and construction of these wires are carefully selected to ensure efficient electrical transmission, making them suitable for applications where reliable data transfer and power supply are essential.
4
Customizable Solutions
Flexible wires are available in various sizes, types, and flexibility levels, allowing engineers to choose the most suitable option for their specific applications. From high-flex wires designed for continuous movement to semi-flexible wires for occasional bending, the range of customizable solutions ensures that each application is appropriately addressed.
5
Space-Saving Benefits
In applications where space is at a premium, flexible wires offer space-saving advantages. Their ability to adapt to the available space reduces the need for excess wiring and bulky cable management solutions. This efficiency is especially valuable in industries like aerospace, where weight reduction and space optimization are crucial for fuel efficiency and payload capacity.
6
Enhanced Durability
Flexible wires are engineered to be durable and resistant to wear and tear. They often undergo testing for mechanical robustness to ensure they can withstand repeated bending and flexing without failing prematurely. This durability translates to longer lifespans and reduced maintenance requirements for the systems they support.
7
Compliance with Standards
Despite their flexibility, these wires are subject to rigorous quality standards and testing. Compliance with industry regulations ensures that flexible wires maintain their reliability and performance, making them a dependable choice for critical applications.
In conclusion, flexible wire is an essential component in a wide array of industries, including aerospace. Its ability to bend, conform, and endure dynamic conditions while preserving electrical performance makes it indispensable for modern engineering. Whether it's powering sophisticated aerospace systems or enabling complex robotics, the concept of flexible wire continues to play a pivotal role in advancing technology and enhancing reliability in various applications.
Advantages of Using Flexible Aerospace Wire and Cable in Aerospace Applications
Flexible aerospace wire and cable offer several advantages over rigid counterparts. Here are some key benefits:
Enhanced Flex Life
Flexible wire and cable are specifically designed to have a longer flex life. They can withstand thousands of bending cycles without degradation, ensuring reliable performance over extended periods.
Reduced Weight
Aerospace wire and cable are subject to strict weight restrictions. Flexible wire and cable solutions are typically lighter than rigid counterparts, contributing to overall weight reduction and fuel efficiency.
Improved Maneuverability
Flexibility allows wires and cables to be easily routed around corners, through tight spaces, and across moving parts. This improves the maneuverability and installation process, saving time and effort.
Resistance to Fatigue
Aerospace environments subject wire and cable to constant stress, which can lead to fatigue failure over time. Flexible wire and cable are designed to resist such fatigue, ensuring long-term reliability and performance.
Resistance to Breaking
The constant movement, vibration, and mechanical stress in aerospace applications can cause wires to break if they lack flexibility. Flexible wire and cable solutions offer superior resistance to breaking and damage.
Materials Selection and Insulation Options for Aerospace Wire and Cable
When it comes to customizing aerospace wire and cable, the selection of materials and insulation options is crucial. Different materials have varying levels of flexibility, resistance to temperature, abrasion, and chemical exposure. Some common materials used for aerospace wire and cable include:
Polyethylene (PE)
Offers excellent dielectric properties, flexibility, and resistance to moisture and chemicals. Suitable for low-temperature environments.
Teflon (PTFE)
Provides high-temperature resistance, excellent electrical properties, and low friction. Ideal for applications where extreme temperatures are encountered.
Fluorinated Ethylene Propylene (FEP) and Ethylene Tetrafluoroethylene (ETFE)
These materials offer excellent resistance to high temperatures, chemicals, and abrasion. They provide flexibility and durability in harsh environments.
Polychloroprene
It is essential to work with a knowledgeable wire and cable manufacturer that can guide you in selecting the most suitable materials and insulation options for your specific aerospace application.
It is essential to work with a knowledgeable wire and cable manufacturer that can guide you in selecting the most suitable materials and insulation options for your specific aerospace application.
Importance of Testing and Certification in Aerospace Wire and Cable Customization
In the aerospace industry, safety and reliability are of paramount importance. Customized wire and cable solutions must undergo rigorous testing and certification processes to ensure compliance with industry standards and regulations. These tests assess a range of factors, including electrical performance, flexibility, resistance to heat and cold, flame resistance, and mechanical durability. Meeting these standards ensures that the wire and cable solutions can withstand the extreme conditions encountered in aerospace applications.
One of the primary concerns when it comes to aerospace wire and cable customization is their electrical performance. These components are responsible for transmitting crucial signals and power within the aircraft's complex systems. During the testing phase, the electrical characteristics of the wire and cable solutions are thoroughly assessed. This includes analyzing their conductivity, resistance, and overall signal integrity. By ensuring the wires and cables meet the required electrical standards, the risk of electrical malfunctions or signal disruptions is significantly reduced.
In conclusion, testing and certification are pivotal steps in the aerospace wire and cable customization process. These procedures ensure that the components meet the stringent requirements of the industry, guaranteeing safety, reliability, and performance. Manufacturers, suppliers, and end-users alike benefit from the peace of mind that comes with knowing that aerospace wire and cable solutions have undergone rigorous evaluation and are up to the task of supporting the critical functions of aircraft.
Maeden High-quality In-house Wire Testing
At Maeden, we understand the criticality of rigorous testing in the aerospace industry. That's why we have an in-house wire testing laboratory equipped with the latest technology and testing equipment. Our dedicated team of experts conducts thorough tests to ensure the quality, performance, and reliability of our wire and cable solutions. We adhere to industry standards such as UL, CSA, MIL-SPEC, and RoHS compliance, providing our clients with peace of mind.
Why Choose Maeden as Your Aerospace Wire and Cable Material Manufacturer?
When it comes to aerospace wire and cable customization, partnering with an experienced and reliable manufacturer is crucial. Here's why Maeden is the ideal choice:
Expertise
With over 40 years of experience in the industry, Maeden has a deep understanding of the specific requirements and challenges faced by the aerospace sector.
Customization
We offer fully customizable wire and cable solutions tailored to meet your specific aerospace application needs.
Quality
At Maeden, we prioritize quality and follow rigorous quality control protocols throughout the manufacturing process. Our wire and cable solutions are known for their reliability, durability, and long lifespan.
Innovation
We continuously invest in research and development to offer cutting-edge wire and cable technology that meets the evolving demands of the aerospace industry.
Customer Support
Our dedicated customer support team is available to assist you throughout the customization process, ensuring a seamless experience from concept to delivery.
Conclusion:
Custom flexible aerospace wire and cable solutions are essential for ensuring reliable performance and longevity in the harsh conditions encountered in aerospace applications. The advantages of using flexible wire and cable, along with the selection of suitable materials and proper testing and certification, are critical considerations. Maeden, with its expertise, customization capabilities, and commitment to quality, is the ideal partner for all your aerospace wire and cable needs. Contact us today to discuss your requirements and discover how Maeden can contribute to the success of your aerospace projects.